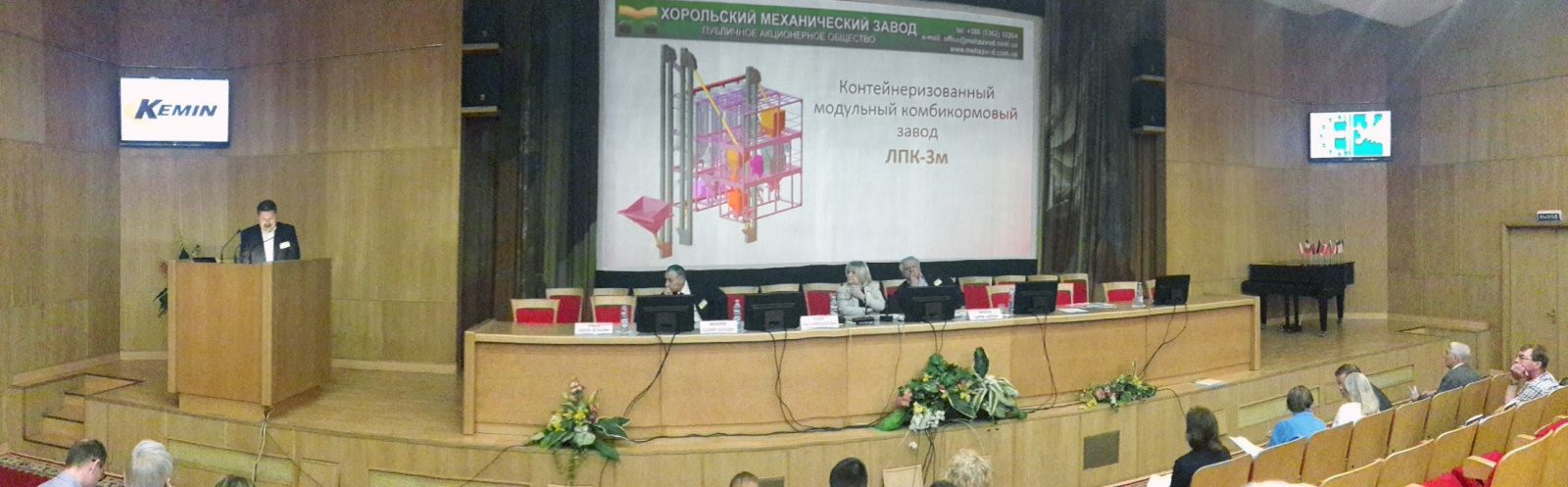
"Комбікорма-2017"
Завод взяв участь в ХI Міжнародній конференції "Сучасне виробництво комбікормів" ("Комбікорма-2017"), яка пройшла з 27 по 29 червня на базі Міжнародної промислової академії. Організаторами конференції стали Союз комбікормщиків, ВНДІ комбікормової промисловості і Міжнародна промислова академія.
Тези доповіді:
Тема доповіді позначена, як «Модульний комбікормовий завод. Швидко. Надійно. Якісно. », але різні виробники вкладають в цей термін різний зміст. «Технекс» називає Модульним комбікормовим заводом той, який складається з «окремих технологічних ділянок. Всі складові елементи оптимально компонуються в кожному модулі, що дозволяє максимально ефективно використовувати наявний простір. Модульний завод розміщується навіть в ангарі, виключаючи необхідність зведення нової будівлі» - цитата з сайту. Ми теж застосовуємо цей підхід, більше 30 останніх комбікормових заводів реалізовано за цією схемою.
Але ми пішли далі, і розробили компоновку заводу, яку Ottevanger, родоначальник цього напряму, іменує як Containerised Mills, яку перекладачі зазвичай перекладають як «контейнерний», що не зовсім точно ... ось міні-завод FaMix 50 від Фінської компанії JPT Industria він контейнерний, тому що повністю скомпонований в 2-х контейнерах з зовнішніми стінами - привіз, поставив один на одного на вулиці, з'єднав і працюй. Правильно, за змістом застосовувати для компоновок Ottevanger – контейнеризований завод, тобто завод спроектований за модульним принципом, модулі якого розміщуються і транспортуються в несучому рамному контейнері. При цьому їх перевезення може здійснюватися, як звичайними євро-фурами, так і морськими контейнерами. Саме такий завод в нашому виконанні був місяць тому запущений в Уганді.
Далі порівняння рекламного буклету Ottevanger і коментарі з нашого реального досвіду.
Ottevanger: «Попередня збірка установок на заводі-виробнику скорочує час установки на місці на 80%, Завод може бути змонтований за короткий проміжок часу» – підтверджуємо, в Уганді завод комбікорму для птиці потужністю до 4т/год, під керівництвом двох фахівців заводу, місцевої бригади з 8-ми осіб, від зняття першого модуля з контейнеровоза і до отримання першої тонни комбікорму - змонтований за 24 робочих дні. І все - бізнес працює, комбікорм реалізується, витрати починають окупатися. Причому цей термін включає монтаж та налагодження двох додаткових модулів-прибудов до основного контейнеризованого блоку виробництва розсипного комбікорму - модуля очищення вхідного зерна і лінії гранулювання.
Ottevanger: «Повний електро-контроль є частиною поставки і може бути розширений до повністю автоматизованої системи», а в нашій базовій поставці - повністю автоматизована система на основі шлюзу даних з вбудованим веб-сервером WebHMI. При цьому власник отримує можливість прямого управління та моніторингу через веб-браузер - по локальній мережі або інтернет з будь-якої точки нашого світу, з будь-якого пристрою - мобільного телефону, планшета, ноутбука, комп'ютера, в т.ч. одночасно з різних місць, без обмеження на кількість користувачів і покупки будь-якого іншого ліцензійного продукту. Звичайно, за бажанням замовника ми можемо реалізувати систему управління застосовуючи провідні SCADA системи - InduSoft Web Studio, або SIMATIC WinCC, які ми використовуємо на більших об'єктах.
Ottevanger: «Контейнерні заводи можуть поставлятися продуктивністю від 1 до 45 т/год. Устаткування встановлюється в 20-ти футові контейнери, які можуть бути встановлені як окремі модулі. Рама контейнера має дві функції. Вона використовується для транспортування, а також, як металоконструкції виробничої будівлі» - все це справедливо і для нашого рішення. Тільки в нашій сьогоднішній лінійці два контейнеризованих модульних комбікормових заводи - продуктивністю до 4 і 10т/год відповідно, але ми можемо за бажанням конкретного замовника виконати в такому виконанні завод будь-якої необхідної потужності і функціональності.
Ottevanger: «Всі компоненти надійні і протестовані. Збірка і перевірка перед відправкою» - все так, ми застосовуємо теж обладнання, яке використовуємо на великих комбікормових виробництвах, це дозволяє виробляти корми відповідно до норм якості ГОСТ і вище. Зокрема, наші горизонтальні скребково-лезові змішувачі дозволяють приготувати комбікорм з однорідністю 95%, що неодноразово підтверджено результатами досліджень на предмет якості змішування в провідних європейських лабораторіях. Причому ці дослідження проводять компанії, які одночасно експлуатують як заводи укомплектування обладнанням Хорольського механічного заводу, так і заводи поставлені Van Aarsen. На нашому сайті ви знайдете копії таких звітів.
Ottevanger: «низькі витрати на транспортування і зручність експлуатації. Економія на будівництві і монтажі» - ну витрати на транспортування можуть бути і трохи вище, теоретично обладнання в розібраному вигляді можна упакувати щільніше ..., але при навантаженні-розвантаженні 40-футового контейнера або євро-фури, в нашому випадку потрібно всього 2 підйоми краном. При цьому зберігання контейнерного модуля на майданчику набагато простіше (і надійніше) купи ящиків і скриньок, які потім ще треба розпакувати...… ну і монтаж – підйом модуля краном відрізняється від затягування окремих елементів обладнання на поверхи.
Ottevanger: «В комплекті з усією системою електрики і стисненого повітря» - все так же.
Ottevanger: «Низький рівень споживання енергії» -але це не залежить від того чи контейнеризований завод.
Ottevanger: «Легко розширити виробничі потужності» - спірне питання, при наявності вільного місця поруч - так, поставивши додаткові модулі, а от замінити змішувач всередині контейнера на більший навряд чи вдасться, на відміну від багатоповерхових схем в потужних приміщеннях. До речі при проектуванні майданчика в Уганді передбачена можливість збільшити продуктивність в майбутньому.
На цьому закінчу порівняння з Ottevanger, чому порівнював з ним - гнатися треба за лідерами, що ми і робимо.
Хотів би акцентувати увагу на одній особливості ЛПК-3м. У складі базового блоку вже встановлено вісім бункерів - це дозволяє в одному рецепті відповідно використовувати при необхідності вісім компонентів. Чотири бункера по 9 кубів для макрокомпонентів - пшениця, кукурудза, ячмінь, соняшниковий шрот - складових в кормі 25% і більше. Загальна вага близько 15÷18 тонн. Два бункера об'ємом 1 куб для компонентів порядку - 5÷10% - висівки, м'ясо-кісткове борошно. Загальна вага близько півтори тонни. Два бункера об'ємом пів куба для компонентів порядку - 2÷5% - крейда, сіль з загальною вагою близько тонни. Таким чином, завод має 3÷4 годинний запас компонентів, який поповнюється за необхідності через завальну яму і норію подачі на чотири основних бункера.
Бункери на 1 і 0,5 куба спеціально виконані таким об'ємом, щоб запас таких компонентів, як м'ясо-кісткове борошно, сіль, крейда, що є швидко злежуваними, не перевищував зберігання більше однієї зміни - 8 годин. Так як ці компоненти, як правило, поставляються в мішках по 20÷50кг - передбачене їх засипання прямо в бункера минаючи завальну яму. В аналогічних, компактних схемах (як би вони не називалися), інших виробників питання бункерів оперативного зберігання компонентів, в тому числі і транспорту з них, який би забезпечував можливість безперервної роботи на заявленої продуктивності, залишається за дужками ціни комерційної пропозиції.
Ціна ЛПК-3м, у виконанні для Уганди продуктивністю 4 тони на годину з додатковим модулем очищення вхідного зерна – 140 000 $ (без урахування грануляції) на базисі поставки FCA Хорол. Вага 27 тонн, тобто 5200 $ за тонну ваги обладнання з несучими конструкціями, включаючи кабельно-провідникову продукцію та систему автоматичного управління з інтернет-доступом, комплектацію мотор-редукторами STROJNA (Словенія), підшипниками SKF (Швеція) і пневматикою FESTO (Італія).
Наше обладнання за своїми технічними параметрами, принципом дії і функціональному призначенню практично не відрізняється від імпортного. При цьому ми даємо замовнику можливість вибору при комплектуванні найбільш важливих деталей і вузлів - з вітчизняного або імпортного виробництва. Незважаючи на те, що надійність нашого обладнання підтверджується реальними термінами служби наших виробів, які значно перевищують розрахункові, конструкція і комплектація наших машин акцентована на ремонтопридатності. Ми застосовуємо в наших машинах стандартні і широко поширені, що випускаються багатьма виробниками - електродвигуни, паси приводу, підшипники, які можна замінити в найкоротші терміни силами експлуатанта. Наприклад, посадочні місця під електродвигуни, дозволяють встановлювати двигуни з різними габаритами. У підсумку, горизонтальні дробарки покупці з Італії беруть у нас без двигунів, а покупці з Росії просять укомплектувати замовлення електродвигунами Володимирського електромоторного заводу.
Коли потенційні замовники з Казахстану запитують, де можна подивитися на працюючий завод, ми в відповідаємо - «Де, де - В Караганді!» - що без жартів? Так, є і там наш завод. З кінця травня на питання де можна подивитися на ЛПК-3м, ми відповідаємо - в Уганді! Упевнений, що протягом року ми зможемо направити потенційних замовників не так далеко.